Additive Manufacturing Goes High End
American Lean Weekday: Leadership | Lean Culture & Intrapreneurship | Lean Methods | Industry 4.0 | Case Studies - Podcast tekijän mukaan Tom Reed: Lean Enthusiast & President of American Lean
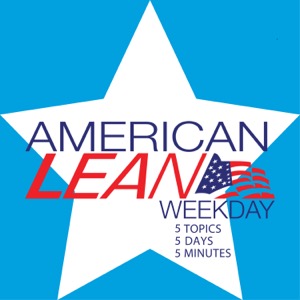
I’m always searching for articles to gather information to share with you regarding Industry 4.0 and other topics. Several weeks ago, I found one that shared how Porsche and Bugatti are using additive manufacturing or 3D printing to make parts for their cars. Additive manufacturing goes high end!Bugatti is using 3D printing to manufacture brake calipers out of titanium. Titanium is a very light, strong material often used in the aerospace industry to save weight.Bugatti is 3D printing these calipers to go on an upcoming $2.9 M car called the Chiron. Current Chiron brake calipers are made from a forged aluminum alloy and weigh 10.8 pounds. The new titanium 3D printed brake calipers will weigh 6.4 pounds. That is 40% lighter.Now don’t go gathering all of your pennies to buy this car- although grocery stores could use the change- these calipers still have to be tested on test cars to see if they will hold up. When you are going the top speed of 261 MPH, you want to make sure you can stop.Porsche is 3D printing parts for many of their older cars. They have been making cars for 70 years and they don’t have parts for many of the older cars which are still on the road.Why are both of these storied companies turning to 3D printing? Let’s understand the benefits vs. typical car part manufacturing. I’m glad I paid attention in engineering classes.1. Casting partsCasting parts allows them to take on different and complex shapes. The engine block in both the Bugatti and Porsche cars was cast using a mold and then machined to meet specifications.Most casting lines that I have seen are very large which means you have to cast a large volume of parts to amortize the investment. You don’t have to cast the same part thousand of times, but you have to cast thousands of parts.2. Forging partsThink of a hammer. The head of a hammer is forged. You can watch it happen in this video.https://youtu.be/JwIpp2uZI6kMolten steel is pressed using large tonnage presses to force the steel into the shape you desire. High tonnage presses, induction heaters to heat the steel, and the molds require large capital investment. Neither Porsche nor Bugatti would make this investment to produce 50 pieces of a replacement part.3. Additive manufacturing (3D printing)The benefit that both companies see in using 3D printing is lead-time and the ability to produce low-volume parts cost-effectively. If you need a part for your 60-year-old Porsche would you rather have it 3D printed or have Porsche set up a line to cast or forge the part?I didn’t think so. Bugatti is working toward designing a part and printing that part the same day, although the brake calipers they are printing take 45 hours.As shown by these two companies, additive manufacturing goes high end!As always, it’s an honor to serve you, and I hope this helps you and your organization get a little better today.Rate and Review HereMore show notes are hereSchedule a free 1/2 call with Tom Reed.Buy the Lean Game Plan