Four Tips to Build a Proactive Culture
American Lean Weekday: Leadership | Lean Culture & Intrapreneurship | Lean Methods | Industry 4.0 | Case Studies - Podcast tekijän mukaan Tom Reed: Lean Enthusiast & President of American Lean
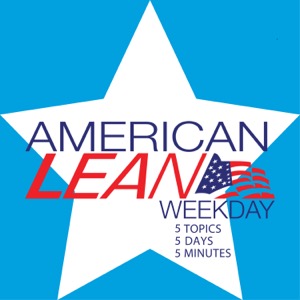
Many company cultures are reactive. People love firefighting. Something happens and then everyone reacts to what happened. Decisions are made with little data collection. I’m sure your company isn’t like that but in case you are, here are four tips to build a proactive culture.1. Establish the company Lean Management SystemWhen you operate without a Lean Management System it is like trying to run a computer without an operating system. Employees aren’t aligned with what matters to the organization.Using a Lean Management System helps guide everyone’s decision making. It reflects the True North of the company. Everyone knows when deciding if it supports the Lean Management System it will support the company culture.2. Hold daily communication meetingsJust last week, I was maturing the communication process with a machine shop. They began having daily meetings in the departments. The next step was to follow standard work for the communication meetings.Holding daily 10-15 minute communication meetings is a great first step to becoming less reactive. Begin by asking each employee if they have any safety issues. Then ask if they have any quality issues.Make each employee answer verbally, yes, or no. Initially, they may not offer much, but as time moves forward, they will share safety and quality issues that you can take care of. Collecting this information goes a long way in helping you build a proactive culture.3. Introduce problem resolution activities to the meetingsAfter about three to six months of conducting daily meetings, introduce problem resolution activities to the daily meetings. This is referred to as daily problem-solving.Begin the process by conducting a Pareto analysis on the quality issues within the department or area. I suggest starting with the most frequent issue first.Collect data to better understand the current condition. Develop a hypothesis of why you think the issue is occurring. Brainstorm improvement ideas. Develop a challenge to reduce the quality issue by a certain timeframe.Then follow a Plan, Do, Check, Act (PDCA) process. Establish what you want to trial. Conduct the trials and learn what happens. If you get the results you are looking for, great! If not, conduct another set of trials and begin a new PDCA cycle.4. Track everything on a communication boardAs you deploy daily meetings and problem resolution activities, track everything on a communication board. This lets everyone know what is going on.If you have maintenance issues that come up during a daily meeting, place the maintenance work order on the board so the employees know it is being taken care of.Show your True North, the data collected and the PDCA cycles completed during the problem resolution. Place the meeting standard work on the board so that each meeting is identical within your company!Using these four tips will help you build a consistent proactive culture across the entire organization.As always, it’s an honor to serve you and I hope this helps you and your organization get a little bit better today.Rate and Review HereMore show notes are hereSchedule a free 1/2 call with Tom Reed.