Using Visual Instruction Sheets to Improve Quality
American Lean Weekday: Leadership | Lean Culture & Intrapreneurship | Lean Methods | Industry 4.0 | Case Studies - Podcast tekijän mukaan Tom Reed: Lean Enthusiast & President of American Lean
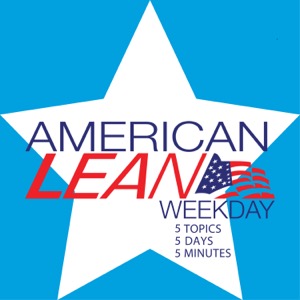
A great way to increase your quality quickly is to develop and deploy Visual Instruction Sheets. Many people, myself included, learn best visually.Let’s make it simple for them to learn how to assemble your product by using Visual Instruction Sheets. Here is what you will gain by using this tool.Benefit 1 – Supports how most people learnIt surprised me when I researched how many people learn visually. The estimate is about 65% of the population. That is a very high percentage of your workforce.Visual Instruction Sheets are simplified drawings. I have seen aerospace companies issue engineering drawings to the floor and then wonder why they have trouble building products.No one can understand the drawings. Give your employees a chance and use these simplified instructions.Benefit 2- Supports ESLUsing pictures helps support workforces where English may not be the first language. Not everyone in your workforce will be fluent in English. Less common, but it still exists, not everyone may be able to read.It is foolish to force a lot of reading upon your employees when you know they might struggle. Simplified drawings will go a long way in making employees work easier.Benefit 3- Makes it easy to improve qualityWhen you deploy Visual Work Instructions, you shade the work with three primary colors. This makes it simple to deploy a check-do-check method of building your products.Work that is colored red is a step that you inspect when it comes to you. You check what the previous operation did. This is called a TQC or Total Quality Check.Work that is shaded yellow is the work you complete at your operation. The Visual Instruction Sheet includes the part number, description, and quantity needed for the operation.Using a number system, you know what order to complete the operations to complete the assembly.When you complete your work you check the work that is shaded blue. This is called a verify. You verify- check your work before moving it on to the next operation.You aren’t verifying everything that you did, just the steps that can be done backward or incorrectly. The work is coded red, yellow, and blue because about 4% of the population is colorblind- mostly male- and they can distinguish between these colors.Benefit 4- Easier to get to Six Sigma qualityBy using Visual Instruction Sheets, color-coded work, and a check-do-check methodology, you can increase your quality levels to six sigma easier than working to increase your sigma levels.Let me explain. People operate at about 1/100 quality levels. If I do something 100 times, I will make 1-3 mistakes. If I do my work at 1/100 quality level, then I check my work at 1/100 quality level, now I am working at 1/10,000 quality level.If the next operation checks my work at a 1/100 quality level, now the process is operating at a 1/1,000,000 quality level. What is that? That is parts per million quality and is approaching a six sigma quality level.It is an honor to serve you, and I hope that you and your company are getting better every day!Rate and Review HereMore show notes are hereSchedule a free 1/2 call with Tom Reed.