What are the Top Compliance Issues Plaguing Medical Device Manufacturers?
Global Medical Device Podcast powered by Greenlight Guru - Podcast tekijän mukaan Greenlight Guru + Medical Device Entrepreneurs - Maanantaisin
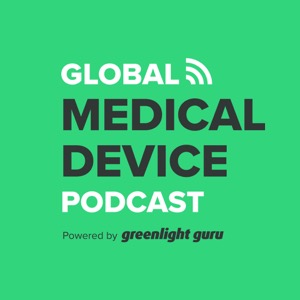
Medical device companies must comply with a list of strict requirements throughout the duration of their product's lifecycle. These compliance efforts will be put to the test once an FDA inspection or ISO audit rolls around. As it turns out, there are a few common culprits when it comes to compliance issues for manufacturers.In this episode of the Global Medical Device Podcast, Jon Speer talks to Tom Rynkiewicz, Vice President of Life Sciences for RA/QA and ASQ Certified Quality Auditor, about the three most common compliance issues and offer answers to questions like, why are the same select areas continuing to cause issues and what’s beyond these recurring compliance issues?Some highlights of this episode include:Based on FDA data, the same issues are the top issues year after year. Are people simply not paying attention to the observations they receive? Are they intentionally not being compliant? Probably not, but then, what are the reasons?FDA does not require medical device companies to share internal audit results that address components of a quality system. Rather than being dishonest, hire an independent, third-party to conduct internal audits. Another issue with internal audits is that only individual components of the quality system are audited. However, when FDA performs an inspection, they inspect the entire quality system - all components combined.The corporate management mindset is to manage complaints and CAPAs. However, the entire process should be built upon having zero complaints. Improve the product, make it safer, make it better quality to not get complaints.The CAPA effectiveness measure is not always effective. Some elements may be good to know, but do not actually measure the effectiveness of CAPAs.FDA audits will find something. Nobody’s perfect, including inspectors. Their ultimate goal is to improve products and safety.Human Behavior: Be honest, transparent, and take a system approach to gain efficiency and true quality culture.Memorable quotes from Tom Rynkiewicz: “Out of just human behavior, they want to help each other. So, they are not brutally honest.”“The second issue about internal audits is they’re auditing individual components of the quality system. When the FDA comes in, they inspect the quality system.”“We all manage our complaints. We manage our CAPAs, and as long as they hit some acceptable threshold, we’re good.”“Shouldn’t the entire process be built upon having zero complaints? The reason we’re doing this is to improve the product, make it safer, make it better quality, so we don’t have to manage complaints.”Links:FDA - Medical DevicesISO 13485 - Medical DevicesFDA - Corrective and Preventive Actions (CAPA)FDA - Case for Quality ProgramFDA - Current Good Manufacturing Practices (CGMP) RegulationsTom Rynkiewicz on LinkedInRaland Compliance Partners